Interviews - QM on kmV Service
Sit-down interview with the Quality Manager for a Blow Molding Plant to talk about kmV's Gate Inspection system and working with kmV.
Quality Manager On kmV's Gate Inspection System and Support
About a year ago, a Midwest bottle blowing plant had kmV install a turnkey vision system tasked with inspecting bottle gates. I recently had a conversation with the Quality Manager at the plant about the vision system and her experience working with kmV. Topics covered include:
- Benefits of Gate Inspection System
- Real-Time Troubleshooting
- Ease of Use
- Remote Access
- Customized Manual
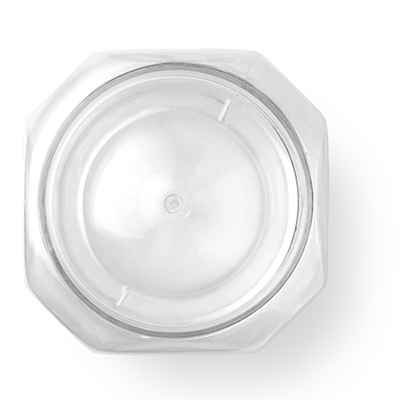
Tell me about the vision system
QM: The one camera inspection system is running on our 48 ounce PET jar line. We were looking for off-center gate and we’ve just added hole (outside the gate region) detection. The system has been working great catching off center gates. In the past week, we have averaged less than 1% failed bottles with about 24,000 bottles daily production. The system’s remote access is very convenient!
The vision system allows us to troubleshoot in real time. It’s helping us pick up tech errors before they become real problems. I’m starting to work on a quick trending report tracking rejects and drifting gate.
Can you talk about Ease of Use?
QM: The vision system is great and I love it. It’s easy to use and easy to navigate and the remote access is super convenient – I’m not stuck futzing with the system by myself.
So you like the remote access feature?
QM: One day, the gate camera alarm was going off showing the camera was not running, but it really was. I got Mike (from kmV) involved. With his help, I downloaded and set up an update and everything is working great again. We don’t have wi-fi access on the floor, but I was able to use my phone as a hotspot.
Understanding what’s happening in training and when you are stuck troubleshooting alone on the floor are two different things. It’s nice to have instant support. Usually, a service call will take hours if not a whole day. We had this fixed in about half an hour.
Can we talk about working with kmV?
QM: I’ve heard nothing but great reviews from managers and folks on the floor. Tim took time during his day off to help me with a problem. Mike, Tim, Jay – we’ve built great relationships with them which is helping greatly. They’re really fast to respond. I love that the manual was made for our specific system. All the screen shots included in the manual are from our machine. The laminated quick reference card that kmV made for us is helping everyone.
Anything else I should know?
QM: Our 48-ounce bottle mold is new. A system like this will really help on lines running older molds.
Interested? Let's get in touch!
If you've got a project that you're working on or have questions about our Gate Inspections or Support Services, contact us today!